Sementoitu karbidi on jauhemetallurgiatuote, joka on sintrattu tyhjiöuunissa tai vedyn pelkistysuunissa, jossa on koboltti, nikkeli ja molybdeeni, volframikarbidimikronikokoisen suuren kovan jauheen jauheen pääkomponentti. Sintrainti on erittäin kriittinen vaihe sementoitussa karbidissa. Niin kutsuttu sintraus on lämmittää tiettyyn lämpötilaan kompakti jauhe, pitää se tietyn ajanjakson ajan ja jäähdyttää sen sitten saadaksesi materiaalin, jolla on vaadittavat ominaisuudet. Sementoituneen karbidin sintrausprosessi on erittäin monimutkainen, ja sintrattujä jätteitä on helppo tuottaa, jos et ole varovainen. Nykyään Chuangrui Xiaobian jakaa kanssasi yhteisen sintrattuun jätteeseen ja syihin.
1. Carbide sintrattu jäte on ensimmäinen kuori
Toisin sanoen sementoituneen karbidin pinta kulkee reunojen halkeamien läpi, vääntymiskuoret tai halkeamat, ja vakavissa tapauksissa pienet ohuet nahat, kuten kalan asteikot, purske halkeamat ja jopa jauhelistaminen. Kuorinta johtuu pääasiassa koboltin kosketusvaikutuksesta kompaktilla siten, että hiiltä sisältävä kaasu hajoaa siinä vapaan hiilen, mikä johtaa kompaktin paikallisen lujuuden vähentymiseen, mikä johtaa kuorimiseen.
2. toiseksi yleisin sementoitu karbidisintrattu jäte on reiät
Yli 40 mikronia kutsutaan huokosiksi. Rakkastoa voivat tekijät voivat muodostaa huokosia. Lisäksi, kun sintrattuissa rungossa on epäpuhtauksia, joita sulaa metalli ei kostuta, kuten suuret huokoset, kuten "puristamaton", tai sintratatulla rungolla on vakava kiinteä faasi ja nestefaasin segregaatio voi muodostaa huokoset.
3. Kolmas yleisin sementoitu karbidistintrattu jätetuote on rakkulo
Sementoituneissa karbidiseostuotteissa on reikiä, ja vastaavien osien pinnalla näkyvät kuperat kaarevat pinnat. Tätä ilmiötä kutsutaan rakkuloimiseksi. Tärkein syy rakkulointiin on, että sintrattu runko on suhteellisen keskittynyt kaasu. Yleensä on kahta tyyppiä: yksi on, että ilma kertyy sintrattuun runkoon ja sintrausprosessin aikana ilma liikkuu sisäpuolelta pintaan. Jos sintrattuissa rungossa on tietyn kokoisia epäpuhtauksia, kuten seosjälkiä, rautajaksoja ja koboltti -romuja, ilma keskittyy tähän. Kun sintroitu runko ilmestyy nestefaasiin ja on tiheä, ilmaa ei voida purkaa. Blisters muodostuu pienimmille pinnoille.
Toinen on, että on olemassa kemiallinen reaktio, joka tuottaa suuren määrän kaasua sintrattuun rungossa. Kun sintrattuissa rungossa on joitain oksideja, ne vähenevät nestemäisen faasin jälkeen tuottavan kaasua, mikä tekee tuotteen kuplasta; WC-CO-seokset koostuvat yleensä seoksen oksidien agglomeraatiosta.
4. On myös epätasainen organisaatio: sekoittaminen
5, ja sitten on muodonmuutos
Sintrattujen rungon epäsäännöllistä muodonmuutosta kutsutaan muodonmuutokseksi. Tärkeimmät syyt muodonmuutokselle ovat seuraavat: kompaktien tiheysjakauma ei ole tasainen, koska valmiiden seoksen tiheys on sama; Sintrattu runko puuttuu vakavasti hiilestä paikallisesti, koska hiilen puute vähentää nestefaasia suhteellisen; Veneen lastaus on kohtuuton; Taustalevy on epätasainen.
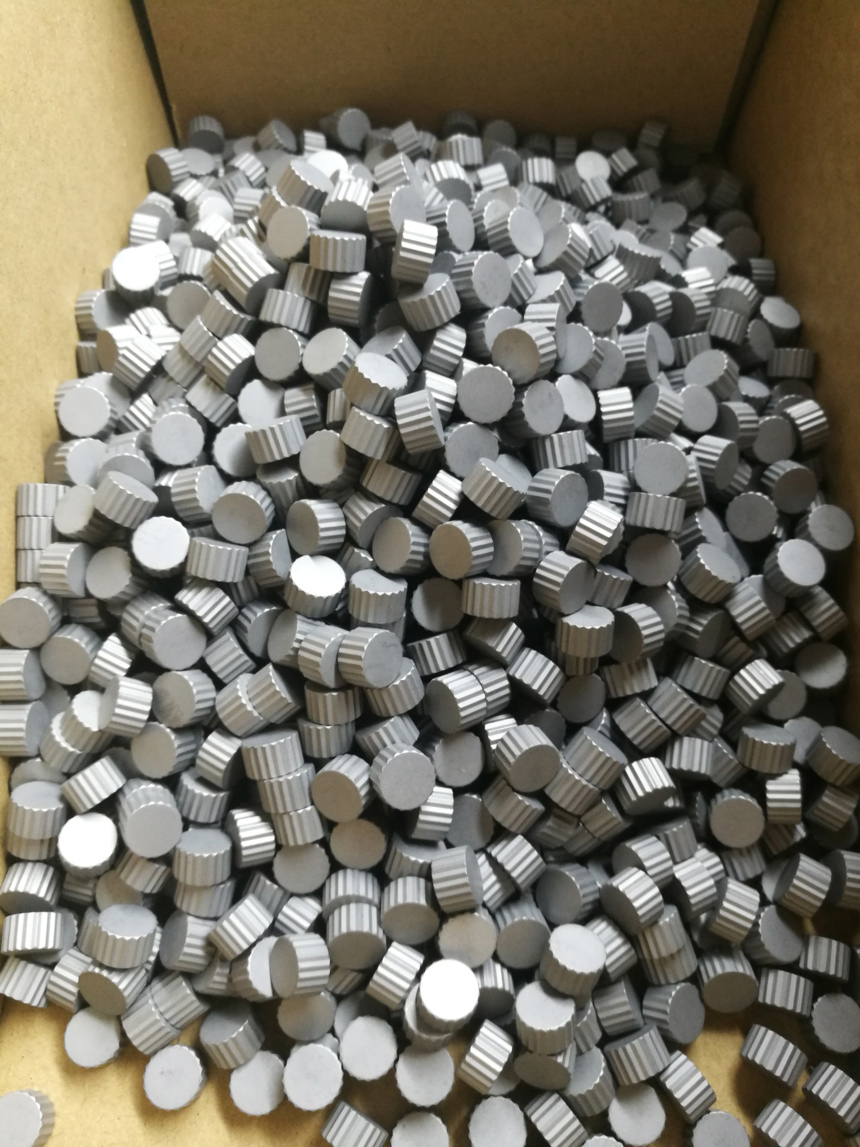
6. Musta sydän
Seosmurtuman pinnan löysää aluetta kutsutaan mustaksi keskukseksi. Tärkeimmät syyt: Liian vähäinen hiilipitoisuus ja epäasianmukaisesti korkea hiilipitoisuus. Kaikki sintratun rungon hiilipitoisuuteen vaikuttavat tekijät vaikuttavat mustien sydämien muodostumiseen.
7. Halkeamat ovat myös yleinen ilmiö sementoituneissa karbide -sintrattuissa jätetuotteissa
Kompressiohalkeamat: Koska paineen rentoutuminen ei näytä heti, kun briketti on kuivattu, joustava palautus on nopeampi sintrauksen aikana. Hapetushalkeamat: Koska briketti hapettuu osittain kuivana, hapettuneen osan lämpölaajennus on erilainen kuin hapettumattoman osan.
8. Ylipolttoa
Kun sintrauslämpötila on liian korkea tai pitoaika on liian pitkä, tuote on ylipolttoaine. Tuotteen ylipoltto tekee jyvistä paksummat, huokoset kasvavat ja seosominaisuudet vähenevät merkittävästi. Alipoltettujen tuotteiden metallinen kiilto ei ole ilmeinen, ja se on vain läpikäytävä uudelleen.
Viestin aika: May-31-2023